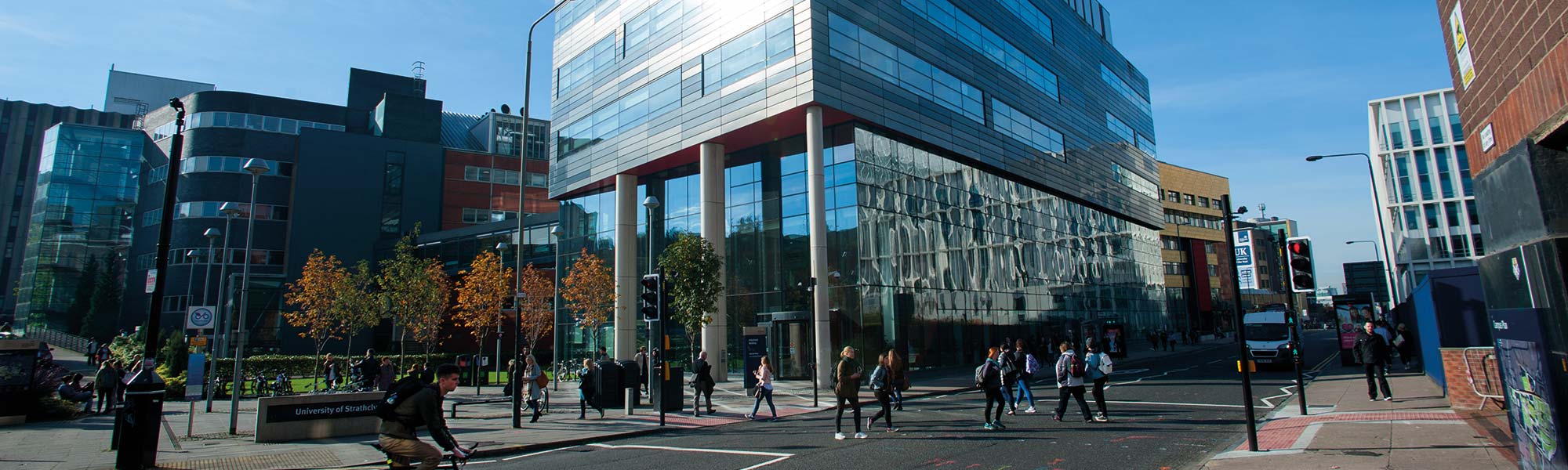
Dr Mohammad Reza Salamati
Manufacturing Engineer
Advanced Forming Research Centre
Back to staff profile
Publications
- AFRC_PRS1760_CRAD_840 Bending Study for Heat Exchanger
- Jadhav Sandip, Salamati Mohammad Reza, Zhao Jie
- (2021)
- AFRC_PRS1759_CRAD_840 UHBR Thermals Heat Exchanger Stacking Fixture Design and Demonstration
- Jadhav Sandip, Zhao Jie, Salamati Mohammad Reza
- (2021)
- Ultra High Bypass Ratio (UHBR) Thermals Manufacturing Trial Outcomes
- Allazadeh Mohammad, Salamati Mohammad Reza, Jadhav Sandip, Zhao Jie, McMaster Thomas
- (2021)
- Absolute Zero : Delivering the UK's climate Change Commitment with Incremental Changes to Today's Technologies
- Ward Michael, Allwood Julian M, Azevedo Jose, Cleaver Christopher, Cullen Jonathan, Dunant Cyrille, Fellin Teppo, Hawkins William, Horrocks Ian, Horton Phillipa, Ibell Tim, Lin Jianguo, Low Hamish, Lupton Rick, Murray James, Clare Adam, Salamati Mohammad Reza, Cabrera Serrenho Andre, Zhou Wenbin
- (2019)
- Microstructure and mechanical properties of Al-1050 during incremental ECAP
- Salamati M, Tamimi S, Moturu Shanmukha Rao, Sivaswamy G, Qarni M, Rosochowski A
- IOP Conference Series: Materials Science and Engineering Vol 194 (2017)
- https://doi.org/10.1088/1757-899X/194/1/012009
- Effect of channel angle on the material flow and hardness distribution during incremental ECAP of Al-1050 billets
- Salamati Mohammad, Qarni Muhammad Jawad, Tamimi Saeed, Rosochowski Andrzej
- The 19th International ESAFORM Conference on Material Forming, pp. 1-12 (2016)
Back to staff profile
Projects
- UHBR
- Allazadeh, Mohammad (Research Co-investigator) Salamati, Mohammad Reza (Principal Investigator)
- 22-Jan-2018 - 19-Jan-2021
- AFRC_CRAD_840_UHBR Thermals
- Jadhav, Sandip (Co-investigator) Salamati, Mohammad Reza (Principal Investigator) Zhao, Jie (Co-investigator) McMaster, Thomas (Co-investigator)
- The Ultra High Bypass Ratio (UHBR) engine thermal management systems project, UHBR Thermals, is a technology research project addressing oil heat management, a key enabler for next-generation UHBR turbofan aero engines. Next generation UHBR engines will be much more efficient than current engines, and will feature a larger fan driven by a power gearbox; a smaller, hotter engine core; a shorter fan case; and a slimline nacelle. These engine technology changes will result in a much larger oil heat load to be managed with a much smaller volume available to mount the equipment, and an increasing amount of heat will have to be managed using air.
UHBR Thermals will develop new thermal management technologies for UHBR engines, and advanced manufacturing techniques to increase the competitiveness of the UK’s thermal systems supply chain. Supported by investment from the Aerospace Technology Institute and Innovate UK, UHBR Thermals brings together a team of recognised experts in thermal management design, analysis, and manufacturing, consisting of: Meggitt; S & C Thermofluids; Manufacturing Technology Centre; The University of Sheffield Advanced Manufacturing Research Centre; the Advanced Forming Centre at the University of Strathclyde; and Cranfield University. UHBR Thermals will be executed over three years from 2017 to 2020, delivering the new capability to the market in time to support the design architecture decision for the next generation engines, which will be delivered to the market in 2025. The UHBR Thermals consortium will be advised by major international turbine aero engine and aircraft manufacturers. - 01-Jan-2017 - 30-Jan-2021
- AFRC_CRAD_94_IAA
- Sivaswamy, Giribaskar (Co-investigator) Salamati, Mohammad Reza (Co-investigator) Bhattacharya, Rahul (Principal Investigator) Walker, F (Principal Investigator) Smith, Bob (Co-investigator)
- The NHS and Pascoe Engineering Ltd wanted to look into a new method of producing accurate custom cranial implants. Their implants currently produce shave a tolerance of about 2mm. They were using a combination of hand tools, rapid prototyping and cold pressing. It takes about 6 weeks to create; it is then followed by anodising and sterilisation. Total time can be over 3 months. In this time the patient wounds can become infected, the skin surrounding the damaged section can shrink which will cause further complications in the recovery process. Using the Incremental sheet forming (ISF) process it is possible to reduce the forming time to less than a few hours (20 minutes to cut the polymer die and 20 mins to form the sheet into an implant), then followed by annealing, anodization and sterilisation. In terms of cost, it can costs over £3k for a custom cranial implant using the current method but less than £500 for implants made using the ISF process. The ISF implants have now received MHRA (Medicines & Healthcare Products Regulatory Agency) certification and can be supplied to hospitals.This has allowed Pascoe Engineering Ltd to step into a new industry and diverge the products and services they offer.
- 21-Jan-2014 - 02-Jan-2015
- AFRC_CATP_Press Brake Forming of AA6082
- Sivaswamy, Giribaskar (Principal Investigator) Salamati, Mohammad Reza (Co-investigator) Devarajan, Nagarajan (Co-investigator) Bhattacharya, Rahul (Co-investigator)
- 20-Jan-2014 - 24-Jan-2014
- AFRC_CORE SHEET FORMING (2013-2014)
- Sivaswamy, Giribaskar (Research Co-investigator) Bhattacharya, Rahul (Co-investigator) Devarajan, Nagarajan (Researcher) Salamati, Mohammad Reza (Researcher)
- Room temperature formability studies on Sheet Metals of following Titanium Alloys:
1.CP-Ti alloys (Ti-50A, Ti-XT and Ti-35A
2. Alpha -Beta Titanium alloys (Ti-6Al-4V and Ti-54M)
3. Near Alpha Ti alloys ( Ti-6242)
4. Beta Titanium alloy (Ti-15-3-3-3) - 04-Jan-2013 - 15-Jan-2014
- An EPSRC Life Sciences Interface Doctoral Training Centre for Medical Devices | Salamati, Mohammad Reza
- Rosochowski, Andrzej (Principal Investigator) Black, Richard Anthony (Co-investigator) Salamati, Mohammad Reza (Research Co-investigator)
- 01-Jan-2009 - 07-Jan-2019
Back to staff profile
Contact
Dr
Mohammad Reza
Salamati
Manufacturing Engineer
Advanced Forming Research Centre
Email: mohammad.salamati@strath.ac.uk
Tel: 534 5555